Furniture has become very much a fashion industry in the last decade and a half, what with Pantone’s color of the year, and popular tones for metal and wood fininshes changing in the blink of an eye. The good news is, just like fashion styles, you don’t have to embrace every new trend that comes along. The same way most women know what fashions look best on them, and change just a few accent pieces in their wardrobe to stay on trend, the same came be done in your home. Continue reading Ch-ch-changes…
All posts by Ellen Dougherty-Saylor
Made In The USA
If you came of age in the 80’s, like I did, you probably remember Bruce Springsteen’s iconic album, Born In The U.S.A., and irritated your parents by loudly singing along to cuts like “Dancing In The Dark,” “I’m On Fire”, “Glory Days,” “My Hometown,” and of course the title track. Many of the songs referenced small town life and America’s manufacturing roots. It seemed to be a simpler time then. Continue reading Made In The USA
Is 50% off the Best You Can Do?
Today we’re going to visit with Mr. & Mrs. Shopper. They are interested in buying a new sofa, and have already decided on a style that they saw online, the SuperSofa. In preparation, they have been reading all the newspaper inserts, and watching the TV commercials. They are especially interested in a 50% off sale advertised by their local Store A. Continue reading Is 50% off the Best You Can Do?
If I Had a Hammer…
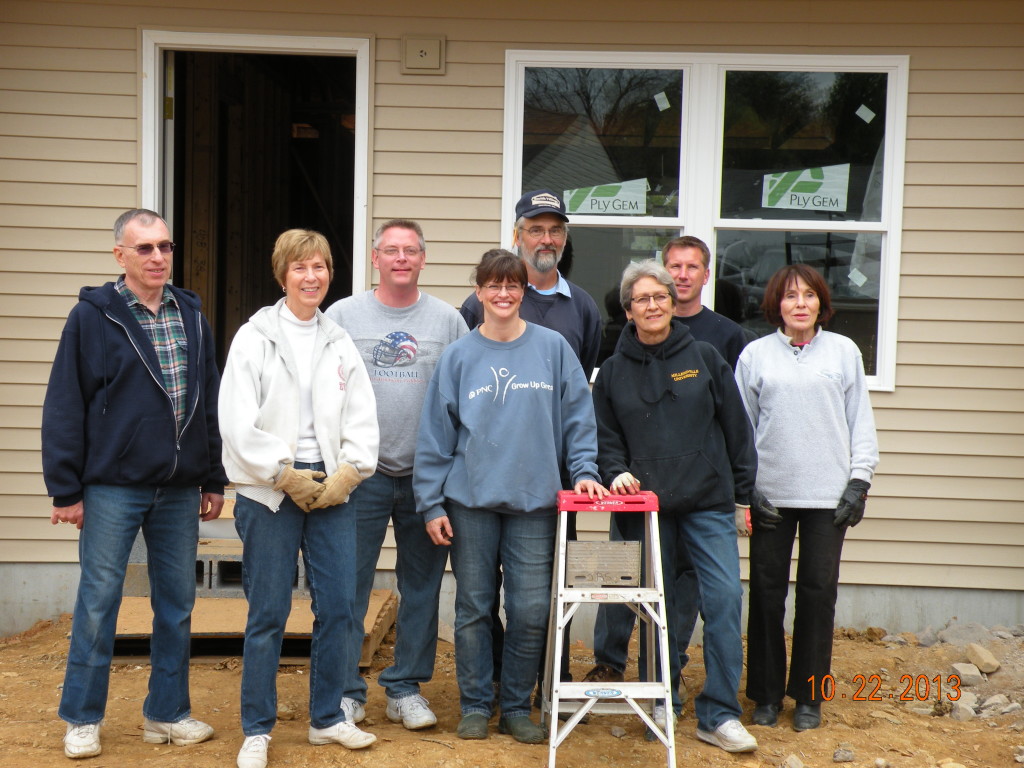
Tuesday, October 22, 2013 was an overcast day with a spattering of rain now and then. It might have started as a quiet morning in Jacobus, most are; but by 8:30 there was enough sawing, nailing and drilling to wake up even the drowsiest of sleepers. It was another workday on Laurie Hanline and her family’s Habitat for Humanity home, and today the volunteers were from Smith Village, right up the street. Because the home is in Jacobus makes it natural that our store would get involved, but it was made even more so as the building lot was a donation from the Smith family. Because of that, all of us at the store kind of look at it as “our” house. We can walk across the street at any time to check on the progress, which has been impressive.
The Smith family (Dale, Anna Mae, Susie and Dallas) all turned out to help; and Bill, Mary, Mark, Jim and I rounded out the team. Our supervisor was Bob, who wasted no time assigning jobs to all of us. He singled out Susie and Mary to be our “cutters.” We were going to be working on the home’s siding and soffit, so their work was crucial. Susie was a little nervous about it. I think her exact words were, “Don’t look at me! I’m not using a saw!” But Bob wasn’t at all put off by her reluctance, and within 15 minutes she and Mary were old pros. Bob chose well – these two were efficient and precise, and kept us supplied with siding and soffit cut to measure for the rest of the day.

Habitat was very lucky to have Jim on the job site that day. With years of building experience, he was able to take over the bending, cutting and installing of aluminum fascia, which freed the Habitat employees to accomplish other jobs too complicated for us volunteers. Jim knew exactly what to do, and I’m sure this allowed our team to complete far more that day than we would have otherwise. In his typical contrary manner, however, he refused to take any credit and just said, “I did whatever needed to be done.” I would have to add that he did it all very well.
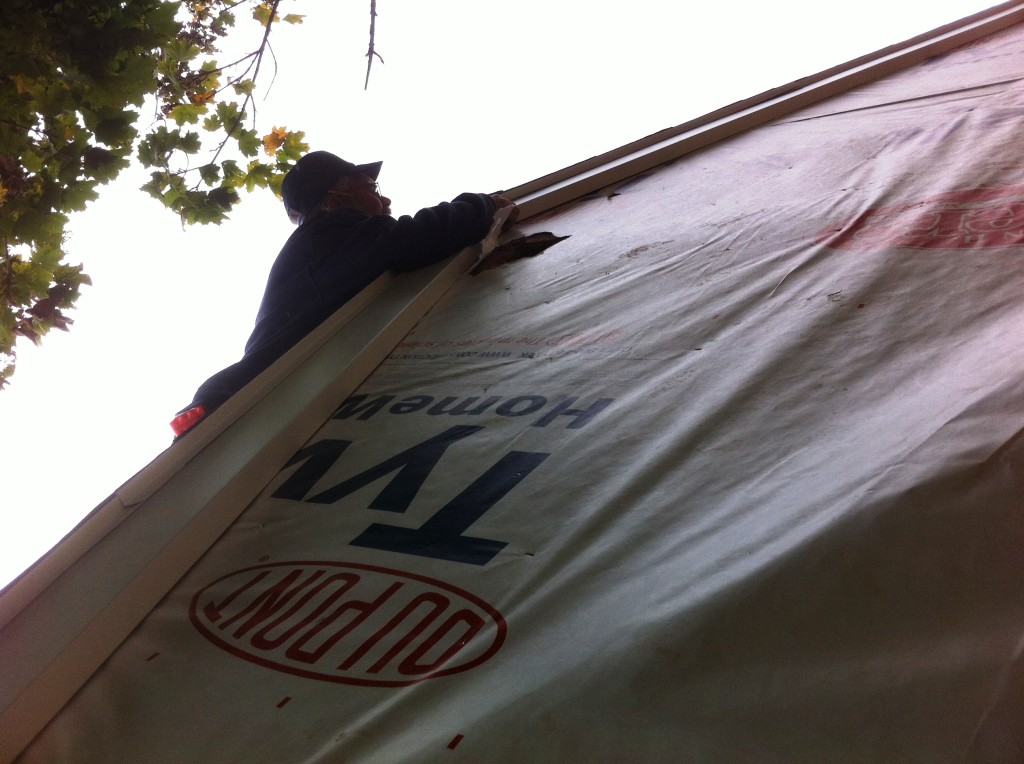
Anna Mae, Dale, Bill and I worked on the siding to the left and right of the garage door. When we reached the top of the door, we realized that the two sides did not line up, and Dale and Anna Mae had to pull off the one side and redo it. Now at this point I was recruited by Bob for a different area, and I didn’t get back around the front until about a half hour later. By then, Bill had managed to unite the two sides seamlessly, and it looked great. I was impressed. Bill was modest. (Like, “aw shucks, me?” modest.)
It made me think how tough it must be for the Habitat for Humanity supervisors to be leading a crew of rank amateurs every day with the good humor and grace that they continually demonstrate. After all, it is up to them to make sure that the work they do is up to code, as well as suitable to the homeowner. They deserve a lot of credit.
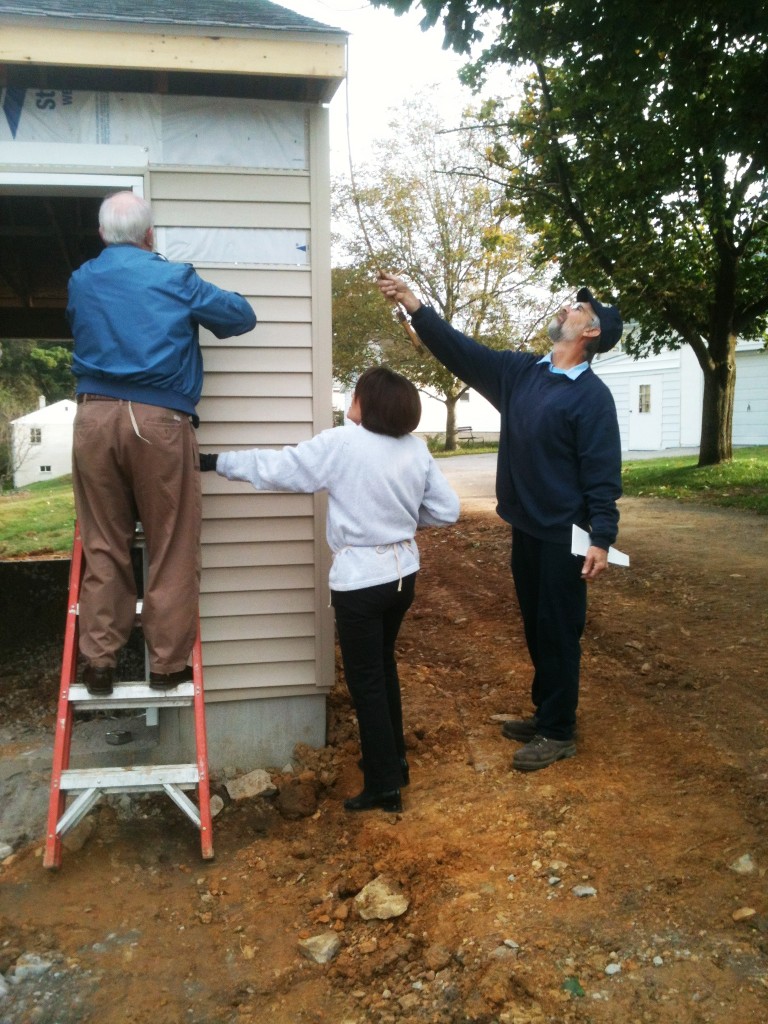
After the masterminding of the garage problem; Bob realized that Bill has had some building experience, and he pulled him off siding to do some of the trickier soffit work. He and a Habitat employee installed soffit all across the front of the house, then Bill moved on to installing J channel, assembling scaffolding and installing nailer boards for drywall inside the house. He made it all look easy.
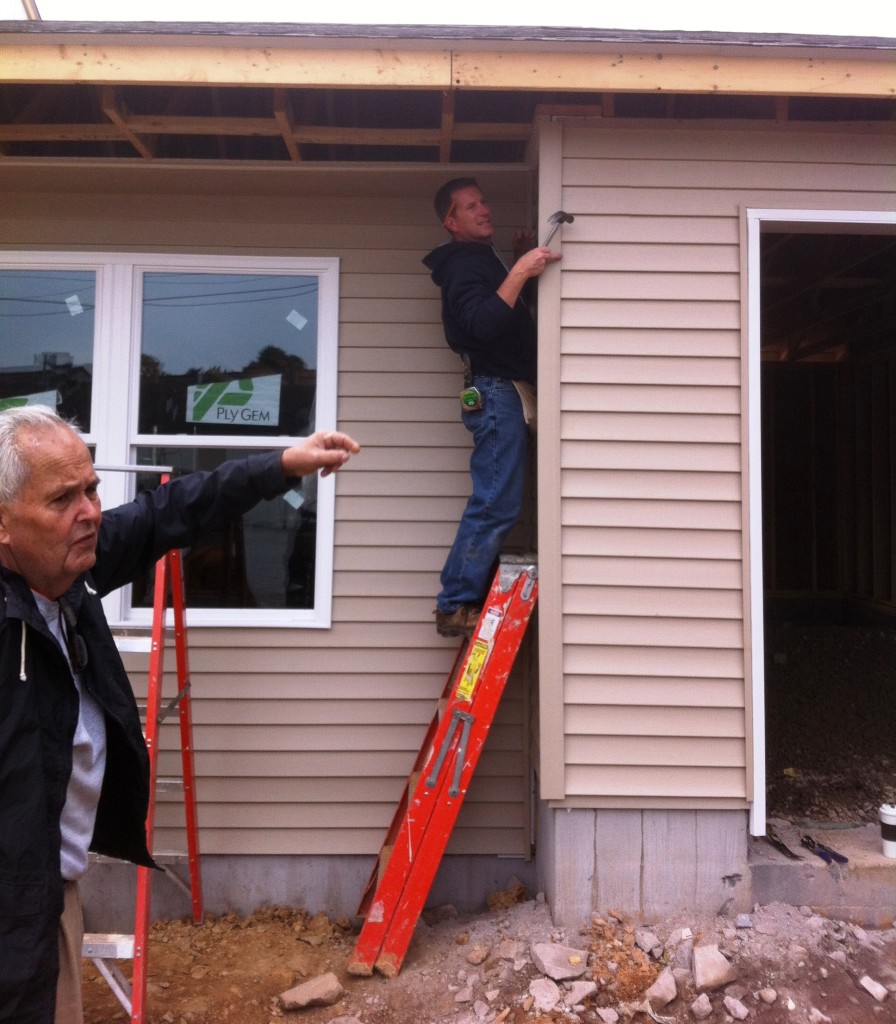
Meanwhile, around the side of the garage, the rest of us were putting up siding, from the bottom to the top. The project was a team effort: measuring, cutting, and nailing. Dallas, Mark and I, and another volunteer named Stephanie hammered away all day; and once we got into the roof peak, Jim came to our rescue and cut all the angle pieces. We never could have finished that side in one day without Jim. Mark says he can now pass for a skilled craftsman, as he didn’t hammer his finger even once, which is more than I can say for myself.
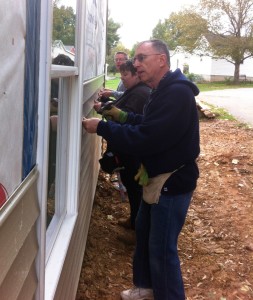
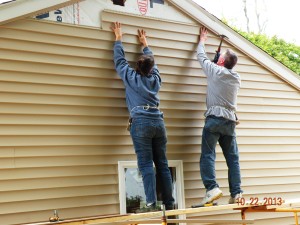
- DONE!
I would be remiss if I didn’t mention some of the behind the scenes players involved with the house. Lance Beard from Beard’s Towing in Jacobus, and Brad Douts of Douts’s Excavating in Loganville did the site work and excavation required to build the foundation of the home, long before the house was anything more than a blueprint. Without their dual effort, there would have been no house for us to work on. Their work is just one example of how the community here in the Jacobus/Loganville area has rallied around Laurie Hanline and her family. Southern York Countians are often characterized as reserved, old fashioned, stick in the muds. Ok, sometimes we are. But we’re always here for our neighbors when they need a hand. Welcome to Jacobus, Laurie. You’re one of us now!
Designed For Kids: We Furnish A Room At Leg Up Farm
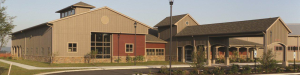
Leg Up Farm is a non-profit therapy center in York County, Pennsylvania, for children with disabilities and developmental delays. They offer many services to their clients, including physical therapy, occupational therapy, animal assisted programs and much more. This year, Leg Up began construction of a new Wellness and Education Center addition to their current facility, which will allow them to expand their services to include aquatic therapy, art therapy, and dance/music therapy. When we were contacted to see if we were interested in furnishing their new Daily Living Skills Area, where clients would learn how to care for themselves in a home environment, we jumped at the chance. We met with Melissa Maley and Tom O’Connor from Leg Up in June to learn what they were looking for and what sort of space we had to work with.
As with most design projects, your plans are usually much grander then the size of the space in which you have to fit them, and this was no exception. They were hoping to fit a single bed and dresser, love seat, end tables and a dinette in the 16′ x 20′ space… and a third of the area was already designated for a kitchen. No problem! We had the rest of the summer to work on the project; completion of the wing wasn’t scheduled until the end of September, at the earliest.
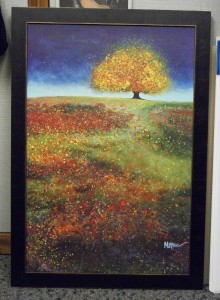
We needed a jumping off place for the design, and found it in a colorful picture of a tree in a field, with blues and oranges. With lots of emails back and forth from Melissa and Tom, we gradually came up with a design that would be accessible, easy to clean, sturdy, and- oh yeah!- attractive! We chose a recycled leather sofa in a cool gray, dark toned wood pieces, and accented it all with blues and bright greens.
In September we got the word that the room was finished enough for us to go and have a first hand look, and off we went to see what we were getting into. Melissa and Tom gave us a tour of the entire facility and WOW! It’s amazing.
Leg Up Farm is the brainchild of Louie Castriota Jr. When his young daughter was diagnosed with a disease causing cognitive and motor function delays, he came to realize that there was no one place dedicated to address the multiple issues of children with special needs. Leg Up offers physical, cognitive, emotional and social support all in one location to help children become better able to function in the community. A look around the facility quickly makes it clear that Louie takes this mission very seriously… virtually everything is interactive and accessible to children with various disabilities. Take a look:
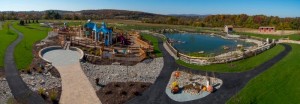

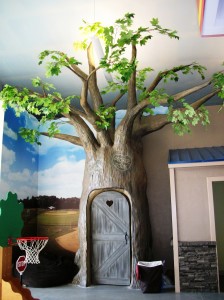
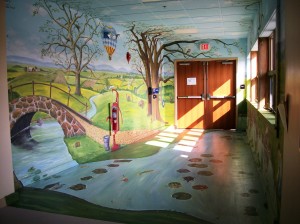
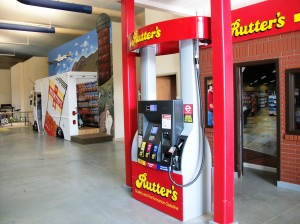
- Aquatic therapy pool.
These few photos are, quite simply, not enough to give an adequate idea of what they have to offer here… I didn’t even take a picture of the stable and indoor riding ring! This is a state of the art facility, and operates strictly as a non-profit organization.
Their mission statement:
…to enrich the lives of families with special needs children
through an effective combination of therapeutic programs and services, education, and advocacy.
In addition:
“We believe every child is special and deserves the opportunity to reach their full potential.”
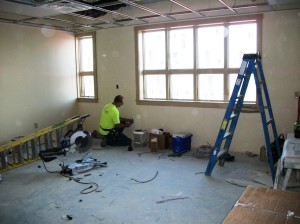
Getting back to our room… it was, well, small. But the windows had a beautiful view of the fields and woods behind the farm. We went back to work energized and awed at the scope of the facility, and our small part in this remarkable place. Everything fell into line, and by the end of September the room was ready, and so were we.
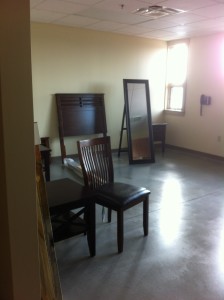
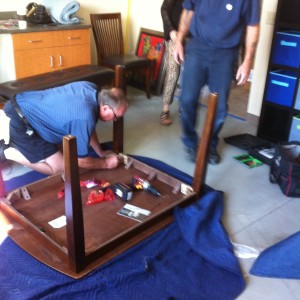
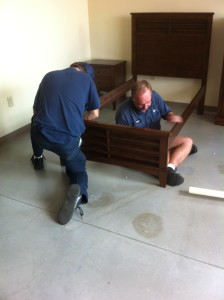
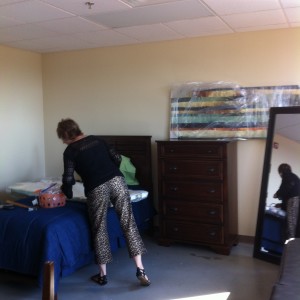
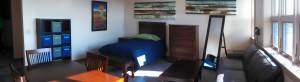
September 26, 2013: one day, 4 people, some nuts and bolts, and voila! We had a newly furnished Daily Living Skills Area for some very deserving young people. We were thrilled at how it all came together, and the Leg Up staff seemed to be pleased as well; which, of course, was the more important part. By the time I write this, children will be getting a chance to use the room, learning all those things they will need to know in order to take care of some of their own needs: cooking, cleaning up, making a bed, doing laundry… those things most of us don’t need to think twice about.
The project was an eye opening one for us. We were filled with admiration for this organization’s effort to provide these kids with the skills and therapy they need to have the best possible chance of living life to the fullest. We’re glad we got to play a part.
Leg Up Farm will be holding an Open House on Saturday, October 19th, 11 am – 2 pm.
For more information go to www.LegUpFarm.org, or call 717-266-9264.
We Welcome Habitat For Humanity’s Hanline Family Build to Jacobus
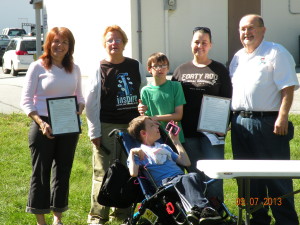
Big doings are afoot in little Jacobus PA. A much talked about story in York County PA of late is that of Laurie Hanline, her family, and Habitat for Humanity’s search for a lot on which to build a handicapped accessible home. They have finally found the perfect location here in Jacobus, on a lot generously donated by the Smith family of Smith Village.
Laurie is a full time student at York College, and full time mom of sons Jacob and Allen as well. Thirteen year old Allen, the only surviving child of a set of triplets, is both physically and mentally handicapped. The doorways in the home they are currently renting are too narrow for Allen’s wheelchair, so Laurie carries him from room to room. Their new home will be completely handicapped accessible, with space for Laurie’s mom, who often provides childcare. The Habitat for Humanity Women Build home will be located on a lovely, partially wooded lot on Meadow Street, with a secluded backyard that has plenty of room for kids to play.
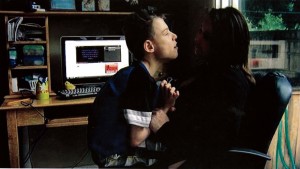
The ground breaking ceremony for the home was on September 7th at 10 am, and in the short space of 3 weeks, excavation was begun and the foundation walls completed. The walls and roof will be put up during “Blitz Week,” the week of October 8-12, and on October 22nd the seasoned crew of Habitat for Humanity volunteers from here at The Village will be back at work, this time just down the street from our store.
It’s a heartwarming thought, knowing that by next year this very deserving family will have their own, fully accessible home. I know that all of us here in Jacobus are proud to be part of such a worthwhile endeavor, and wish all the best to Laurie and her family in their beautiful new home.
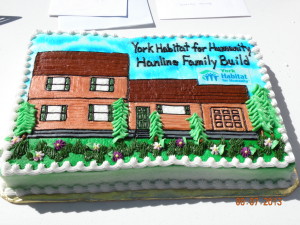
Smith Village will be offering a discount in the amount of your sales tax to any customers who make a donation of $5 or more between October 3 and October 20. You can also contact Habitat for Humanity at 854-6168 to donate or volunteer, or visit their website at http://yorkhabitat.org/
Don’t judge a sofa by its cover, and other useful advice.
If you’ve ever gone sofa shopping, you’ve probably seen what appear to be two nearly identical sofas, but one costs hundreds of dollars more than the other. Is the less expensive sofa just a much better deal? The answer is inside. Because the majority of a sofa’s construction is hidden, it can be tough to make a call on quality just by appearances. Here are some things to look for, and questions to ask your salesperson:
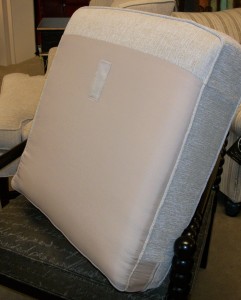
Check the underside of the seat cushions. One trick manufacturers use to keep the price down is to use a less expensive fabric on one side. A cushion like this cannot be flipped over to decrease wear on the fabric. If your sofa will be used heavily, this can make a big difference in the life of the upholstery.
The frame inside the sofa is what provides most of the support. Frames can be made of many materials… make sure you ask your salesperson how the frame is constructed on any upholstered piece you are considering. The best frames are made of hardwood, and joints are both glued and screwed together for durability. Plywood also makes a sturdy frame, because the different layers of wood are bonded together with the grain running in opposite directions which reduces warping and cracking. Particleboard, chipboard or composite wood products are not nearly as strong, as they are made of small pieces of wood pressed together. They break down much more quickly because of this.
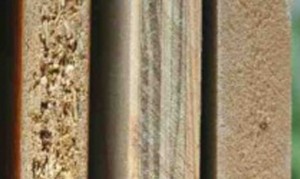
In the base of the sofa frame is the decking. This is what the seat cushions rest on. The gold standard is 8 way, hand tied coil springs. These make the seat more resilient. This kind of spring is very labor intensive to make, and many are now machined “tied” with metal. In a mid price point sofa, sinuous springs are often used. These are “S” shaped. A better sofa will have these more closely spaced to provide more support, and the edges will be “double-sprung,” meaning two sinuous springs are placed close together where the decking meets the arm of the sofa. This prevents the cushion from collapsing in towards the arm. A less expensive sofa may only have webbing to support the seat. This is not as strong, durable, or resilient as the other 2 methods.
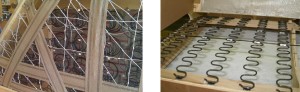
Cushion material is the next thing to consider, and a lot depends on the firmness you prefer when sitting. Those who like to lounge with their feet up often prefer a softer seat, while those who sit upright are more comfortable with a firmer cushion. Because of this, make sure that when you are shopping, you sit on the pieces the way you sit at home. A good cushion starts with a good quality piece of foam. Foam comes in different densities. A high density foam will hold up longer, but will make a firmer seat. Most manufacturers will add a wrap of fiberfill or down on the outside of the foam to provide more cushioning. Down makes for a cushy seat, but can cause a rumpled appearance in the upholstery fabric. Some cushions will have springs inside the foam, and this will increase the longevity of the cushion.
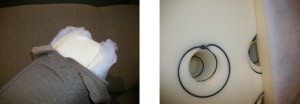
The inside back of the sofa supports the back cushions. Springs here are a better choice than webbing for the same reason as in the decking.
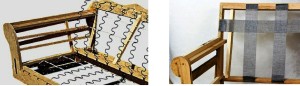
Back cushions may be either a piece of batting wrapped foam, like the seat cushions, or loose fill. A foam based back cushion will be firm, and is often used in a tight-back sofa, where the fabric on the inside back is upholstered directly to the sofa frame. A loose cushion back (where the cushions are completely removable) or a semi-attached back (where they appear to be removable but are still attached to the frame in some way) can have either a foam cushion, be made completely of loose fiberfill, or a combination of both. These types of back cushion will have much more give than a tight back.
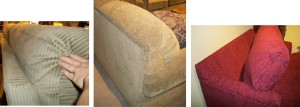
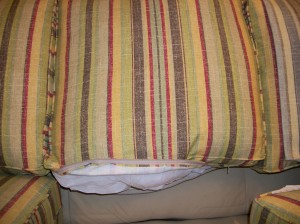
None of the 3 types is better as far as quality, it depends on your preference. A tight back has a neater appearance, loose and semi-attached backs have a more casual, rumpled appearance. Fiberfill backs do occasionally need to be fluffed… look for zippers on the the cushion so you can redistribute the fill, or add more.
The fabric is the most visible part of the construction. Upholstery fabric is one area where price does not necessarily indicate quality. Some designs are very expensive to weave, but may not be very durable. Others, such as microfibers, are cheap to produce but are very strong and stain resistant. Upholstery fabric is graded by the manufacturers to indicate durability. Your salesperson should be able to give you this information.
Now that you know what to look for in a good quality piece of upholstered furniture, here is something else to consider. Some people think they should spend less on their family room furniture than they do for the less busy areas of their home, since it’s just going to get abused. In reality, you should spend more for your family room furniture… so it will hold up better to the tough conditions there. In less heavily used rooms, such as living rooms, you can get away with less expensive furniture, since it won’t be used as hard, and attractive upholstered furniture is just as likely to be inexpensive as it is expensive, because, as you now know, all the value is on the inside.
Thank You…
The other day I was compiling customer comments from our Delivery Quality Surveys, and it really gave me a warm glow. Anyone who has worked in the retail business for any length of time knows that customer complaints are part of the territory. People who are dissatisfied with a product or service for which they have paid can be very vocal about it. Satisfied customers, on the other hand, may tell a few others about a good experience, but they don’t often come back to you to thank you for, essentially, just doing your job. So when people do thank you, it really hits home. Every customer to whom we deliver furniture receives one of these Delivery Quality Surveys. Filling it out and sending it in is optional, though a stamped envelope is provided. We use these surveys to see our business through our customers’ eyes, and make improvements where they are indicated.
Just a few excerpts:
“Smith Village is a ‘jewel’ tucked away. So glad we stopped in to take a look.”
“You have amazing staff from sales to delivery.”
“Set the standard for delivery – great job!”
“It was wonderful to experience such OUTSTANDING customer service in a day and age where customer service is almost nonexistent. I will definitely be a repeat customer.”
“We had done quite a bit of shopping around before we found Smith Village. Yours was the best experience for us. The price and quality of both furniture and service professionals was terrific.”
Obviously, there are clients we could not make happy. As the saying goes, you can’t please all of the people all of the time. But to hear such generous praise from any of our customers is a heartwarming thing.
It’s nice to hear we’re doing our job.
Thanks.